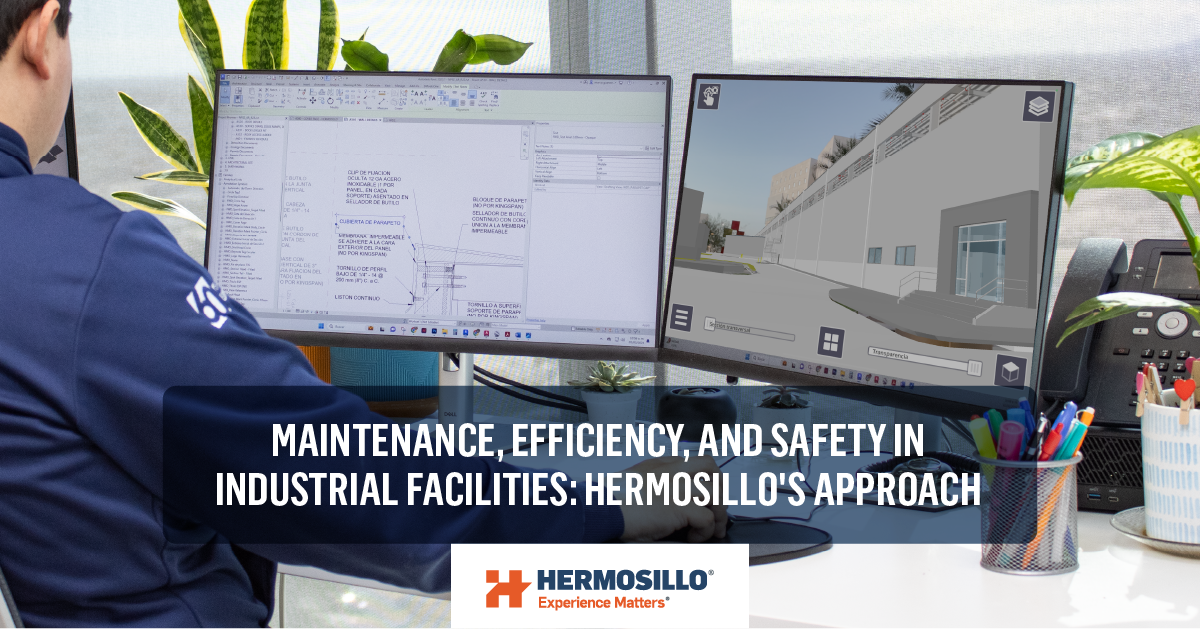
Our passion at Hermosillo is turning our client’s visions into reality by providing innovative and efficient solutions that drive operational efficiency and industrial safety.
In this blog post, we’ll discuss a fundamental topic for the long-term success of any industrial facility: maintenance. We don’t just focus on designing and building cutting-edge facilities; we also support our clients’ buildings by maintaining them in optimal conditions throughout their lifecycles.
Industrial Facilities Maintenance
We understand that industrial maintenance is much more than occasional repairs. It’s a comprehensive strategy, part of our safety culture, encompassing preventive and predictive maintenance. Preventive maintenance, in particular, plays a crucial role in extending equipment lifespan, preventing costly breakdowns, and ensuring worker safety.
At Hermosillo, we integrate maintenance into all phases of our projects, from initial planning to final delivery. By sitting down with our clients at the project’s outset to define their needs, we create a personalized preventive maintenance plan based on our high-precision 3D models. This allows us to prevent incidents by identifying and addressing potential issues before they become emergencies, ensuring continuous operational efficiency of the facilities.
Our ability to design projects in 7D allows us to go beyond conventional expectations. By working with LOD350 or LOD400 models (level of design), we can provide our clients with advanced tools to manage the maintenance of their facilities more effectively. From preliminary construction sequence simulations to energy efficiency analyses, our solutions are designed to optimize every aspect of the facility’s lifecycle.
Additionally, we work closely with our clients to integrate building models into their asset management systems, such as 360 Ops and SinguFM.
- 360 OPS is a solution for managing maintenance and assets. It allows general contractors and building owners to realize the value of BIM in construction operations.
- SinguFM is a secure, cloud-based software platform for managing facilities, properties, and commercial and industrial real estate assets. It is designed to increase the value of properties, tenants, and owners.
- Autodesk Tandem is the next-generation platform for building operation and maintenance management, focused on leveraging BIM model metadata through digital twins.
By using these systems, we facilitate the supervision and maintenance of facilities.
Clash Interference Detection
Clash interference detection is fundamental in ensuring long-term quality, operational efficiency, and safety in industrial facilities maintenance. At Hermosillo, we understand that even the slightest clash between facilities and building components can have significant negative consequences. Therefore, during the design phase of our projects, we implement a rigorous strategy to avoid interferences and simultaneously ensure the correct conditions for end users to work safely during the project’s operational phase.
Using advanced tools such as Autodesk Navisworks or ACC Model Coordination, we conduct a meticulous collision detection process. This allows us to identify and eliminate any potential interference between various architectural and MEP (mechanical, electrical, and plumbing) trades, ensuring that industrial facilities are free of obstacles and can operate optimally.
By generating clash-free federated BIM models, we guarantee smooth and trouble-free construction and lay the groundwork for more efficient and safe maintenance in the future. By avoiding conflicts from the initial design stages, we minimize the risk of breakdowns, optimize costs, and extend the project’s lifespan.
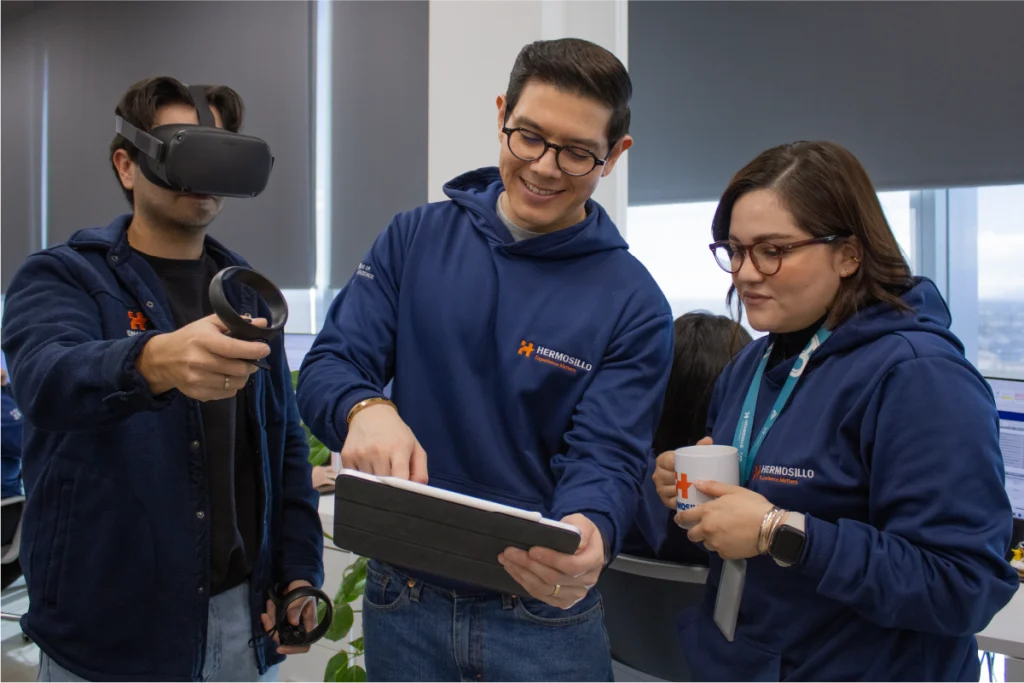
Lean and BIM Integration in Hermosillo
The integration of Lean and BIM in Hermosillo goes beyond the design and construction phases, significantly impacting the management of industrial infrastructure throughout its lifecycle. Since 2018, we have embraced Lean Construction as an essential part of our corporate culture, applying the “value-driven delivery” methodology in all our projects.
This synergy between Lean and BIM translates into a proactive approach to industrial facilities maintenance. Our team of BIM Managers, certified as Scrum Masters, works closely with the Lean Construction team to implement Lean design frameworks, such as Scrum, which allow us to optimize resources and accelerate the pre-construction phase.
By focusing on waste reduction and delivering exceptional value to our clients from the project’s early stages, we lay the groundwork for more efficient and sustainable maintenance in the future. Furthermore, weekly sprint meetings allow us to identify and proactively address potential issues affecting the facilities’ operations and safety.
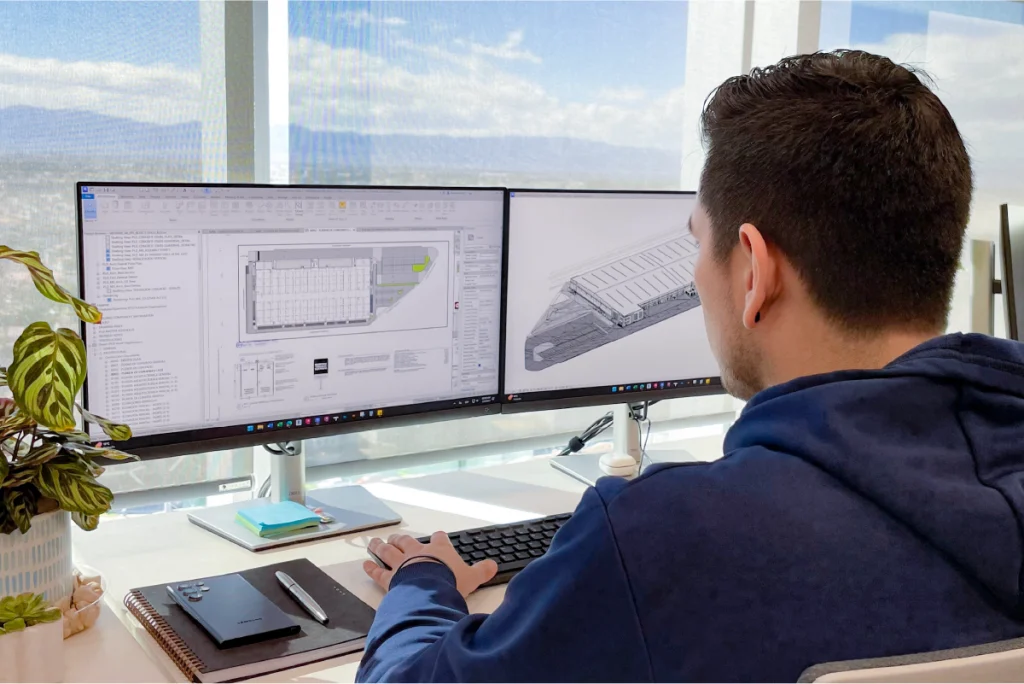
Conclusion
In Hermosillo, we firmly believe in the importance of industrial maintenance for the long-term success of any company we work with. Integrating Lean and BIM is a strategy to ensure timely and budget-compliant delivery of our projects and a tool to optimize industrial infrastructure management and guarantee optimal performance over time.
That’s why we strive to exceed expectations and offer innovative solutions that drive operational efficiency and safety at every stage. With Hermosillo, you’re building world-class facilities and investing in a safer, more efficient, and sustainable future for your company. Trust us to take your most ambitious projects to the next level.