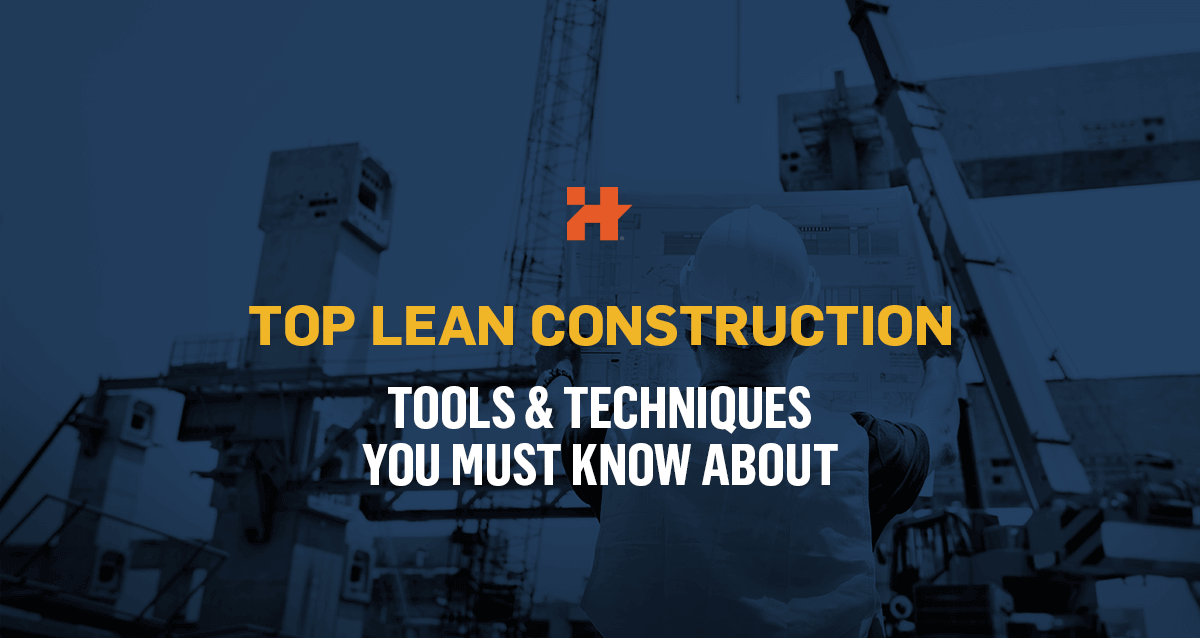
Although a well-established Lean Construction culture relies heavily on the mindset of its people, some tools can facilitate the process. We refer to Lean Construction Tools as every technique or methodology that makes Lean thinking easier. Therefore, by thinking in a lean way, you are going forward to the right path.
There are around +50 tools you can use. But, the biggest challenge is to know which one will help you more according to your specific situation. You may have problems with Jobsite logistics, but you’re doing OK in ahead planning, and so on.
That’s what we are trying to help you with. In this post, we will list the leading and most essential tools, and what can you do with each one. We will also give you some advice on best practices based on our experience with lean planning methods.
What are Lean Tools? : Identifying the goal of each tool
In general, any lean construction tool will lead you to enhance the value of your project. It’ll be likely to be through the removal of waste, such as transportation, overproduction, inappropriate processing, lead time, inventories, rework, or unnecessary movements in construction processes. As you may know, eliminating waste is critical.
What kind of waste are you trying to eliminate?
There are three ways of seeing waste according to a crisp paper named “Waste Processing Framework For Non-ValueAdding Activities Using Lean Construction.” Hence, we will list the tools in this way:
- Waste Detection
- Waste Processing
- Waste Response
Tools for Waste Detection
Value Stream Mapping
We refer to VSM as a flowchart that illustrates the steps to deliver a product or service. This one has being useful for quite a long time now. One of its first appearances was on the 1918 book called Efficiency Methods, by Charles E. Knoeppel. Later this diagramming was used at the Toyota Production System. Even though it wasn’t called VPM just yet.
It was until the 1990’s when the term gained popularity.
The tool works by making a flowchart for the visual representation of a process. Therefore, the technique relies on analyzing the flow of the process. The diagram is designed to highlight improvement opportunities.
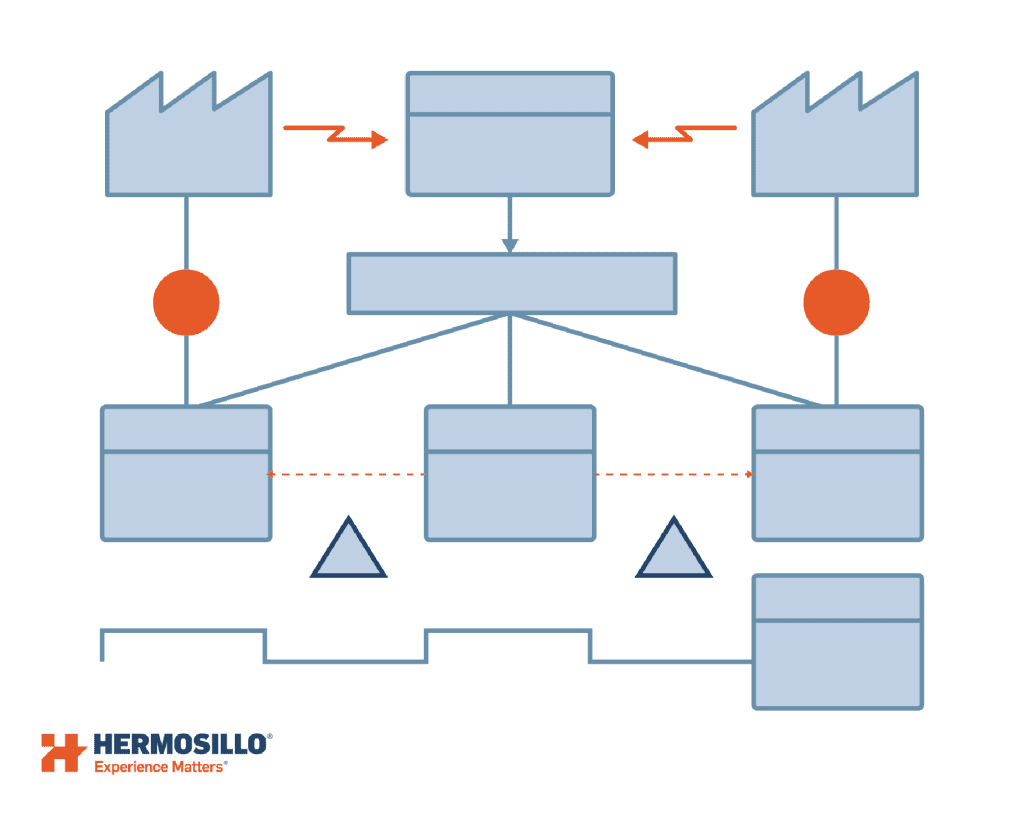
Benefits: You clearly can see which steps are adding value and which aren’t. You can see problems like process delays, excessive downtime, constraints, and inventory issues.
Construction Process Analysis
This technique was created from the need to detect waste in the construction industry. Process models in construction were not designed to distinguish between value-adding and no-value adding activities accurately. Consequently, this lean construction tool was made to identify waste in processes.
The process chart records each step of a construction operation. It may include the sequential steps that the worker, part, or material, goes through.
For better understanding, the chart uses symbols for operation, transportation, storage, delay, volume inspection, and quality inspection.
Main goal: “To investigate the overall flow of steps in a process and provides a method to improve the flow diagrams common among process analysis techniques.”
The ultimate goal is to eliminate these: waste, irrationality, and inconsistency. Among other things, the use of CPA is to identify waste associated with unnecessary processing; people move, material moves and waiting time.
Benefits: You can clearly see the process. Although it works better in repetitive assignments, it can be used at any time, with no special preparation or tools required. It’s a simple method. A particular advantage is that workers on-site can easily participate in analyzing their processes.
Tools for Waste Processing
Five whys
Five whys is a quality management tool for problem-solving that tries to find the root of an issue. It establishes that workers should be asking why five times until they identify the underlying nature of the problem.
The essence is to continually question why a particular problem happens until you have the “core” cause. The process is to ask ‘why’ 5 times (or more if necessary) whenever you identify a problem. As a result, you may end with a wholly unexpected source.
Keep in mind that all the answers must be based on facts and real data, not emotional opinions.
Main goal: Dissect a problem and reveal its underlying causes.
Benefits: It’s a great way to collect feedback from the team. It’s also a handy technique to focus resources on high-value activity.
Pareto Analysis
Vilfredo Pareto created this analytical tool to graphically illustrate the Pareto principle, also known as the 80/20 rule. Which helps you realize that the majority of results come from a minority of inputs.
The tool is useful in lean construction because it helps to analyze data about the frequency of the causes in processes. It visually depicts which situations are more critical.
The later is achieved by placing the bottom x-axis in order from largest to smallest. The y-axis has the quantity or cost. Often, a line is drawn against the different y-axis to represent the cumulative impact %.
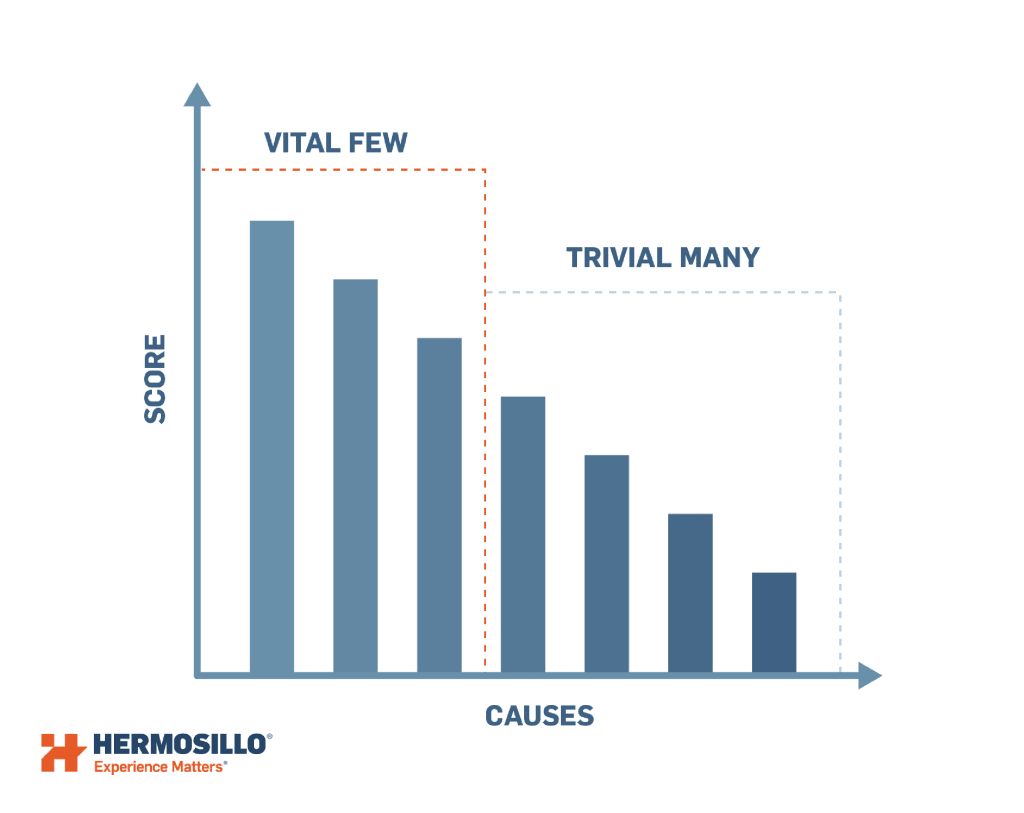
Benefits:
- See the process’ problems at a glance
- Understand quickly all of the factors working against the process
- Concentrate on the issues that cause the most significant disruption
Tools for Waste Response
5S
This “tool” is a process for waste removal from the workplace through the use of visual controls. 5S stands for the Japanese Seiri (Sort), Seiso (Straighten), Seiton (Shine), Seiketsu (Standardize), and Shitsuke (Sustain).
Each “S” has a different objective.
- Seiri means to identify unnecessary items in the workplace.
- Seiton, on the other hand, looks to arrange each object so that anyone can find it.
- Seiso means keeping the work area clean and in the right condition.
- Seiketsu consists of building procedures to maintain the last 3 “S.”
- Shitsuke means turning into a habit the fact of maintaining the correct procedures
Main goal: Order and efficiency at the job site.
Benefits: It increases people’s involvement, teamwork, morale, health, and safety; it reduces costs, variability, and uncertainty; and it helps in setting the basis to implement Lean Construction in any company or project.
Last planner system
The Last Planner® System of Production Control (official name), could be one of the most known lean construction tools. You may even have seen it in pictures with the colored post-its. However, it is so much more than that. The Last Planner system is a crucial tool for lean planning and execution.
Most importantly, is that it provides the necessary support for working towards planned accomplishments. In other words, it marks a path and the actions that must be done to follow that path. And most importantly, it features times and following tasks that an effort needs to be able to start.
For this reason, LPS incorporates “pull planning” principles, where only the work that can and will be done is considered. It also follows lean construction principles such as JIT and Value Stream Mapping.
To be clear, LPS was developed to make planning processes and work flow highly reliable, and to build necessary trust within a collaborative team environment. The key is to involucrate every team player to make the most accurate planning possible.
Now let’s get into specifics.
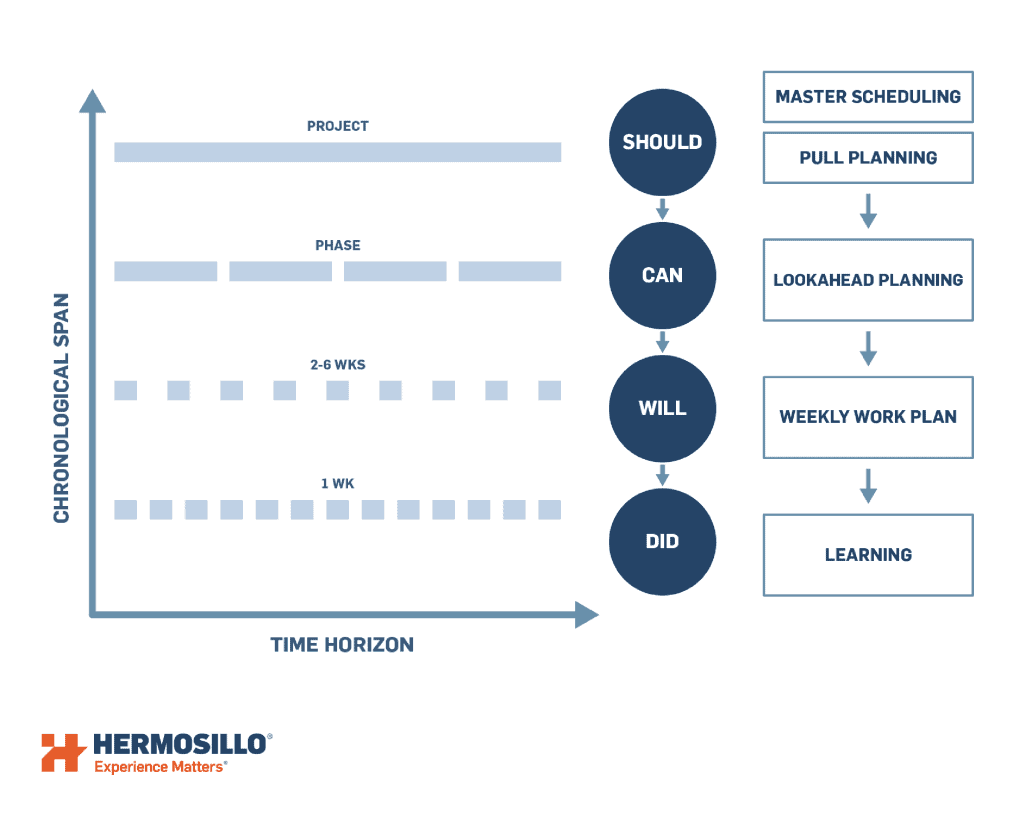
On the other hand, Pull Planning (or Phase Scheduling), is for strategically planning segments of work to produce progressively elaborate Weekly Work Plans.
Thirdly, we have lookahead planning. It focuses on ensuring that work can be done.
Then we have the weekly work plan, where the tactical team collaborates to plan each day’s work. The point of maximum progressive elaboration to create reliable work plans. (What Will Occur)
The fifth part focuses on learning from what the team did.
As you can see, each level down is more detailed than the past one.
Wrapping up
Ultimately, these are the lean design process tools and techniques that we think can be universally useful. Nevertheless, there’s a whole world of valuable techniques that may help your lean culture. Lean, it’s just getting started!
If you’d like to see some of our efforts in lean construction, click here.