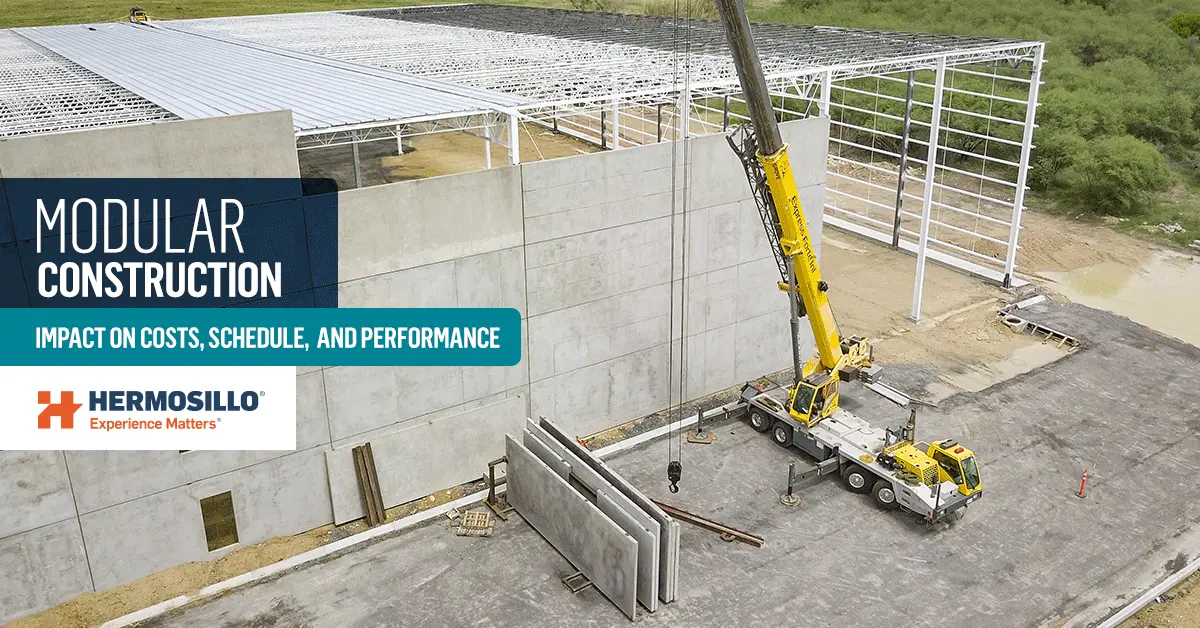
Efficient and smart construction is about bringing simplicity into a complex setting. We like to describe it as the LEGO® building game brought to real life to create fully functional buildings. But as you may know, simple is not exactly easy.
Modular construction has been around for a long time and is now experiencing a renaissance. Now, you can masterfully map the design and logistics by utilizing BIM frameworks and a LEAN Construction mindset, resulting in an enhanced experience. In this blog post, we will go through everything modular construction means, our experience with it, and its impact on costs, schedule, and overall project performance.
But first, let’s get the definition right.
What is modular construction?
Modular construction refers to a method of building structures where components, known as modules, are prefabricated off-site in a controlled factory environment. These modules are then transported to the construction site and assembled to create the final building. This approach offers several advantages, including increased efficiency, cost-effectiveness, and faster project completion times.
We can describe modular construction as building off-site and assembling on-site. It’s like taking specific components you’ll do in a traditional construction into a factory, away from the fuss.
Those components can vary from a simple precast wall to a completely functional room of a 10-story hotel building. These elements are built off-site in a controlled environment. Then, they are transported to the project location, where they will be assembled into one beautiful building.
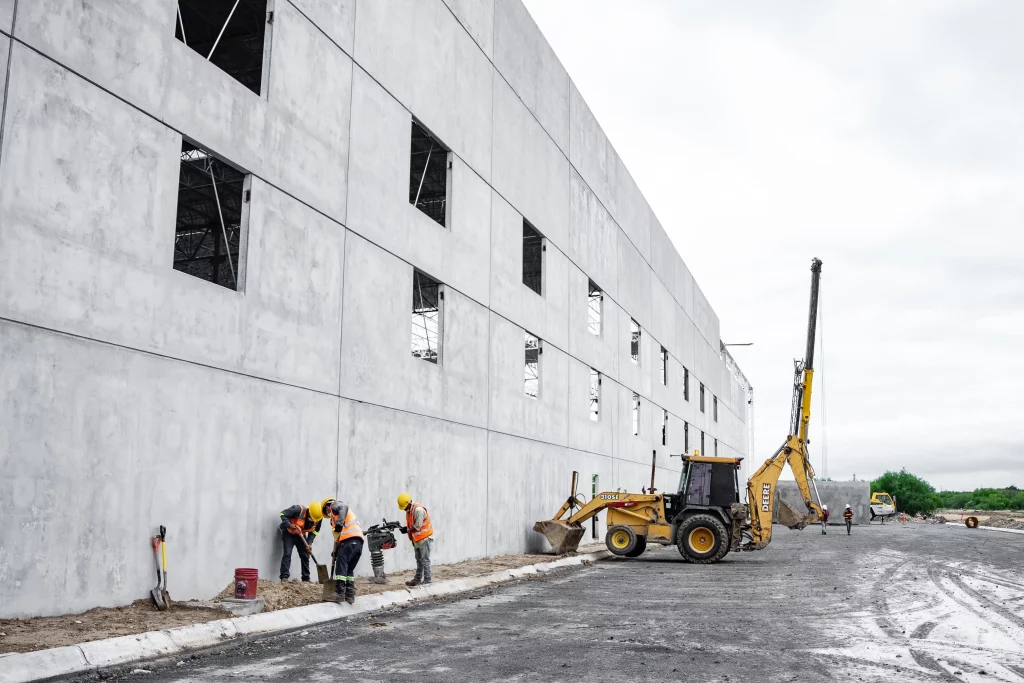
But how does modular construction work?
The process is quite simple.
As implied previously, they are roughly four stages for completing a modular construction project; design, production, transportation, and assembly.
- Design development: This is the phase where robust planning takes place. In modular construction, the elements must be designed ahead, freezing as much as possible in order to ensure the fabrication of the correct elements, ready for their assembly. In traditional construction, design can go through many changes in a cycle, even during the construction process. The importance of avoiding redesign processes seeks the complete benefits of modular elements.
- Module components production: The project starts to come to life. Once the design is finished, with the final blueprints and specs, the manufacturer may begin production. Scheduling with the design team will help to define which project elements need to be done in advance to follow up on assembly needs.
- Transportation: In this phase, the finished components are loaded in a vehicle to be delivered to the construction site. This one may sound like an easy step; however, it’s one of the trickiest.
Transportation can get complicated depending on the volume of the finished product. Sometimes the logistics of shipping capabilities, local size, load restrictions, and distances will determine the element’s dimensions and design. - Assembling: This is the end of the puzzle, where everything makes sense. Once the modules are delivered at the construction site, contractors start the module installation. They include connections for MEP (mechanical, electrical, and plumbing), exterior and interior finishes. Ending up with completing external systems, such as roofing components, or internal spaces, like lobbies.
While traditional and modular construction share similar planning and design processes, crucial differences make the latter more challenging. For starters, modular construction requires more coordination between teams due to much off-site work.
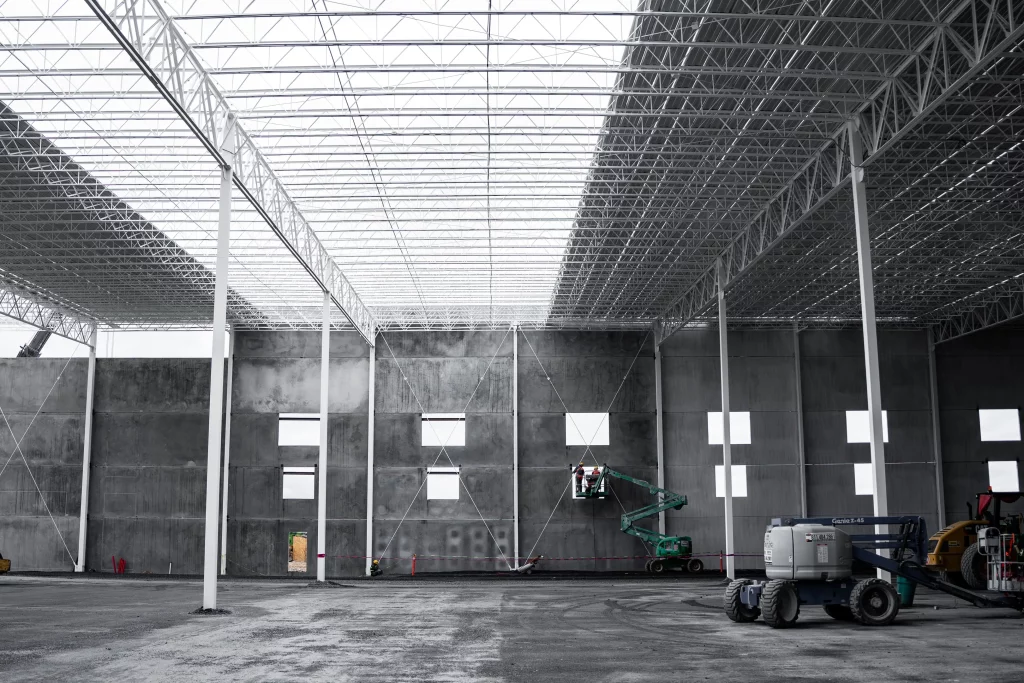
What are the types of modular construction available?
It is essential to know that not every project is a candidate for this kind of process.
There are projects that, due to specific characteristics in their design and space needs, benefit significantly from the nature of modular construction. According to a survey conducted by Dodge Data & Analytics, contractors, architects, and engineers consider the following industries the most likely to succeed in applying a modular construction approach.
- Healthcare
- Hotels
- Multifamily
- College buildings
- Office buildings
- Schools
- Public buildings
- Commercial warehouse
- Manufacturing buildings
- Retail stores and shopping centers
Considering that you can apply modular construction to a wide range of industries, it is also worth knowing that there are different types of modular construction. There could be either volumetric or non-volumetric components.
For example, a non-volumetric unit could be a panel, a frame, or a precast wall, as opposed to a volumetric one, which could be an entire bathroom floor. The volumetric ones are those that you could assemble as LEGOS® on-site. Non-volumetric units require more work on the construction site because they are connected once there.
To further understand, let’s dive into what we do best: precast walls.
Our experience building precast walls
Precast walls are a type of modular construction that involves creating panels or walls by pouring concrete into a reusable mold or form. This definition may sound a little familiar to the one we use to describe Tilt-up walls, but the main difference is that precast walls can be fabricated off-site. This characteristic makes them particularly special when the project’s needs focus on quality, a particular panel design, short execution schedules, or dealing with constantly changing conditions.
This type of construction has brought our clients a wide range of benefits:
We worked with Grupo AVANTE to build multiple warehouse and logistics facilities under this regime. We created precast walls and insulated them off-site, obtaining advantages such as:
- Shortened delivery times: we fabricated the walls in a remote location we started the project foundations simultaneously.
- Streamlining of wall assembly: the installation was very fast, as we assembled in average, eight walls a day.
- Space Availability: The main building structure remained clear without space restrictions, as the walls didn’t need to be kept on the construction site (as opposed to the Tilt-up system).
- Integral quality: Every wall was made with the same strict quality standards, as we severely inspected them on the manufacturing site. One of the benefits of their products in a controlled environment is that it allows the final product to be isolated from weather, rust, or corrosion conditions.
- Perfect finish: The assembled walls deliver long-lasting and durable authentic-looking facades with low-maintenance costs.
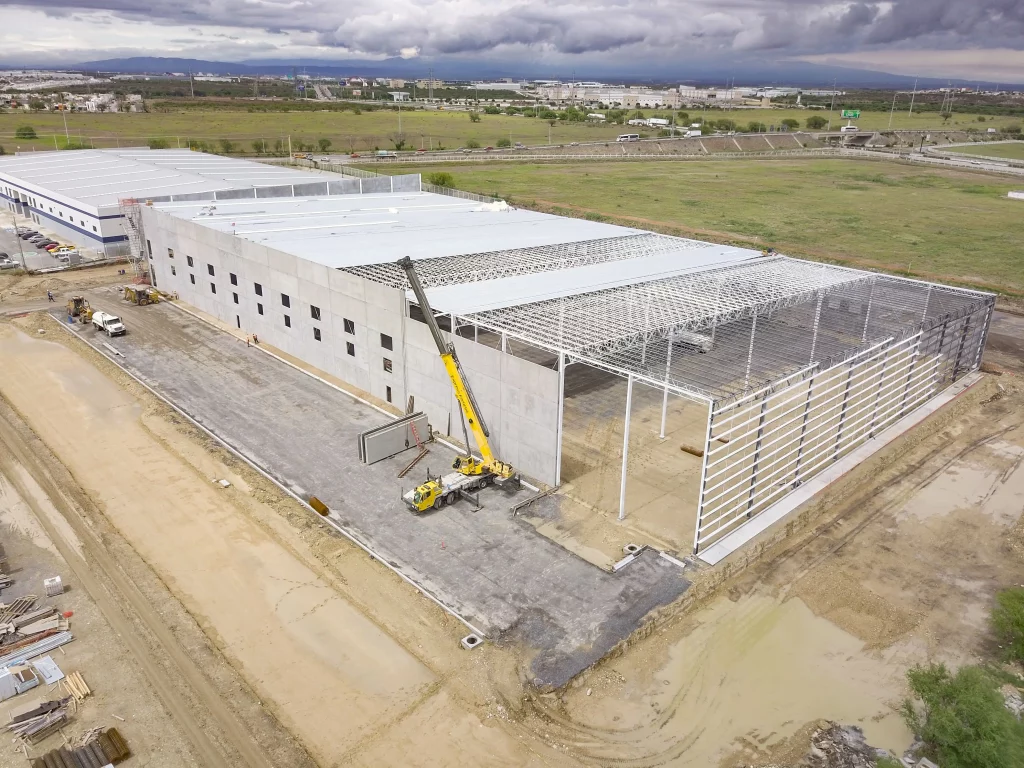
So considering all of the above, is modular construction worth it?
The impact of modular construction: challenges and benefits
To fully experience the benefits of modular construction, you must choose wisely the project to apply it. This type of construction is a problem solver. However, according to research conducted by McGraw-Hill Construction, this approach can increase the overall quality, shorter delivery times, and offer more predictable costs when implemented effectively.
So with this in mind, let’s start. We will explain the impact on costs, schedule, safety, sustainability, quality, and benefits.
- Costs: 60% of surveyed companies said that they considered Modular construction improved budget performance. According to another study, you could save up to 20% on costs. Still, you also risk increasing them up to 10%. We will explain these two outcomes below. Keep in mind that this is data from the United States. In Mexico, it may vary by project.
- Gaining 20% of cost savings would mean you did everything right. These savings could come from:
- On-site labor: Modular construction reduces project schedules, so the pay wage of construction management reduces overall by 20%.
- Redesigns savings: With LEAN Construction methodology, BIM, and the intensive planning that you must forgo for a modular construction setup, means you can avoid those rework costs.
- The 10% increase can be caused by the following:
- Logistics: To keep costs regulated, you must consider the distance between the manufacturer and the destination, the timing when finished to when needed on-site, and the size and weight of your modules.
- Materials: Material costs may increase if you need some to produce a shippable product.
- Factory costs: Depending on the setup, allocated factory costs can make up between 5% and 15% of total expenditures on a construction project.
- Gaining 20% of cost savings would mean you did everything right. These savings could come from:
- Schedule
- The more work you complete off-site, the more significant your time savings. You can start the building in the manufacturing facility while still working on the foundation or structure on-site. Instead of being a linear process as in traditional construction, you can work simultaneously, causing time to reduce drastically.
The key is to avoid additional storage costs and deliver the fabricated modules just in time when the onsite construction is ready.
Schedule optimization allows for coordinated and repeated activities. Also, the construction work on site is overly simplified from traditional builds because it consists mainly in assembling.
3. Safety:
- According to the U.S. Labor Department Bureau of Labor Statistics, rates for fatal injuries are, overall, substantially lower in manufacturing than in traditional on-site construction. Working in a controlled environment poses a safer workplace. They estimate that accidents are reduced by over 80% relative to site-intensive construction.
4. Sustainability:
- Less work in an open space means more control, which leads to less waste. Greener construction sites because there is less waste production.
- Due to part of the building taking place inside a facility, noise is diminished by 30 to 50%!
- Another positive impact is that construction site visits are reduced by up to 70%.
- Modular construction significantly impacts construction conditions, and environmental control during construction can contribute to attaining LEED credits.
5. Quality
- The monitored manufacturing setting allows the production and control for a high level of quality and consistency. Also, an enclosed facility results in reduced exposure to weather, which can affect the health of the components or materials.
6. Productivity
- Lastly, productivity mainly improves with three actors working simultaneously: BIM, LEAN Construction, and the modular construction approach. Planning is key. So, considering that the work plan is efficiently and rigorously mapped out, everyone knows their responsibilities and when their work is expected to be delivered
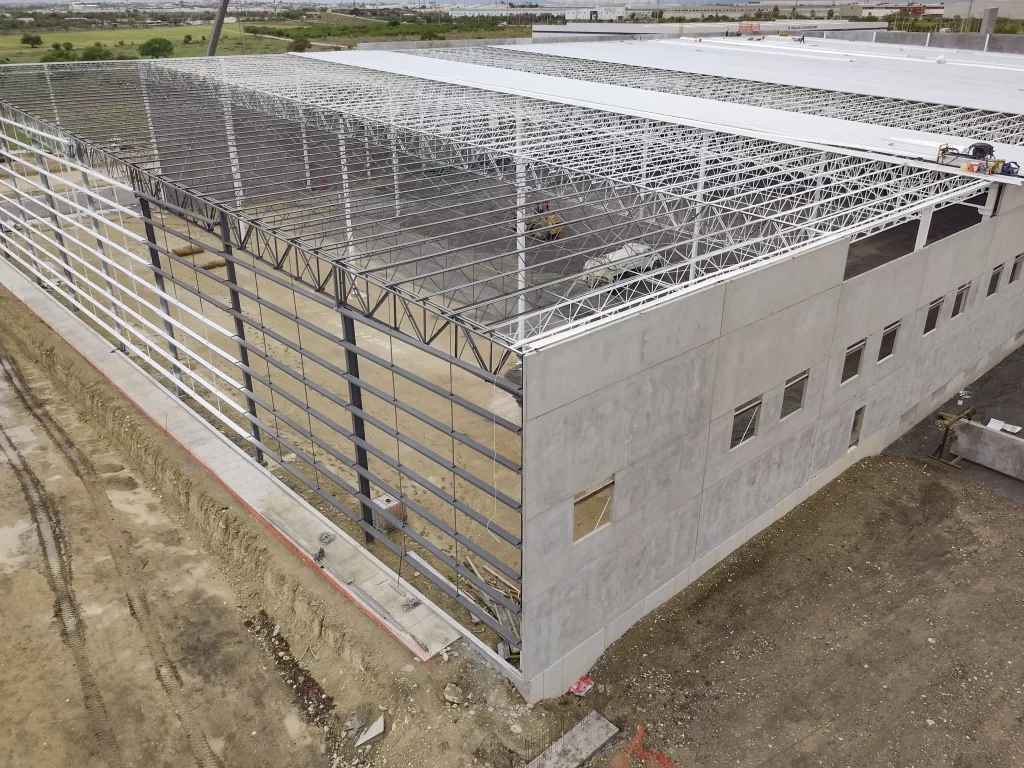
Wrapping Up…
Modular construction is at its peak. There hasn’t been another moment in history where modular construction has performed as well as it does now. Technology and innovative construction management solutions have brought a new light to it, allowing contractors to experience the benefits of this type of construction fully.
But, as the ever-changing nature of the industry has proven, no solution fits every project. Modular construction is an excellent option in the broad toolbox of contractors. You must identify the challenges you will face and select the accurate means to help you solve them.
In our experience, building with this methodology has brought our clients tangible benefits in quality, schedule performance, positive environmental impact, and incremental cost control.