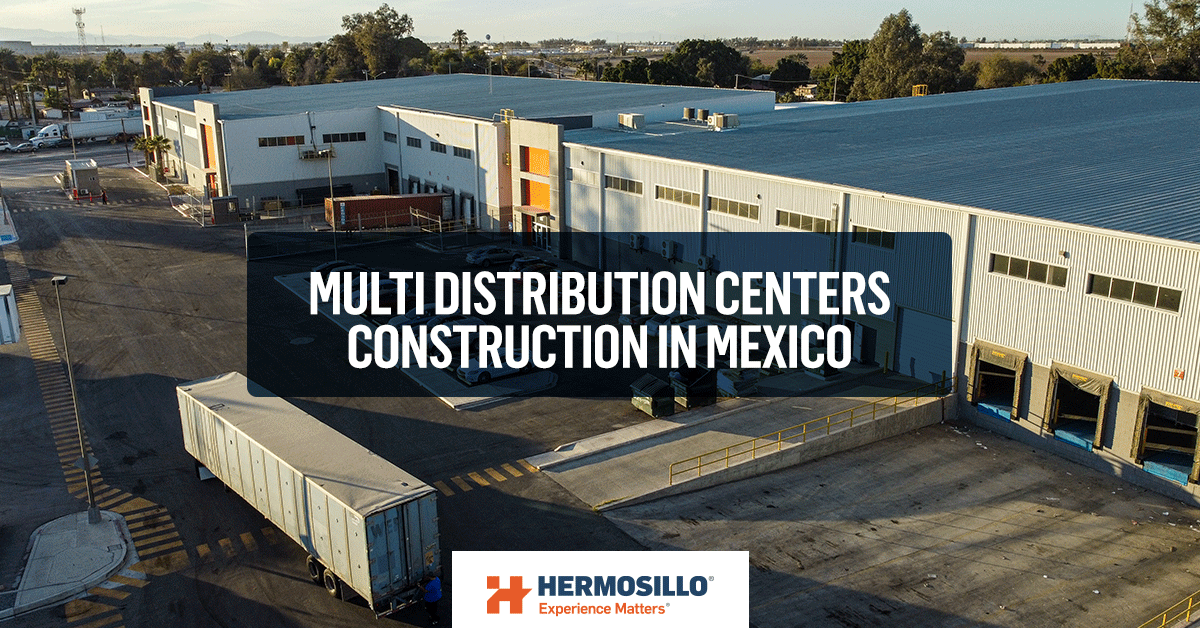
E-commerce is growing quicker than ever. Businesses have to increase their competitiveness and productivity in order to stay afloat. Due to the COVID-19 pandemic, in 2020, online shopping reached a value of $316,000 million pesos in Mexico. This resulted in a growth of 81% compared to 2019.
Because of this, retail and wholesale businesses have seen the need to have better, closer, and more efficient distribution centers to fulfill their orders on time. In this post, you’ll find valuable information about the construction of logistic centers for different industries, as well as success stories of the projects where we have worked on.
4 CHARACTERISTICS OF A CORRECTLY DESIGNED & BUILT DISTRIBUTION CENTER
The optimization of a logistics warehouse is reflected in its operations and starts from the design and construction of its infrastructure.
To increase operation productivity in distribution centers, it is important to consider the following building characteristics: floor quality, clear height, clear span (distance between columns), and the overall width of the warehouse.
1. Floor quality:
- A good distribution center must have the perfect interior floor, capable of withstanding the intensive use of forklifts and the weight of the racks where pallets with the product are stored so that the floor has high durability and does not suffer premature damage.
- The interior concrete floor must have the correct flatness so that forklifts and/or the different types of autonomous robots work around with no problem. In the case of forklifts, accurate flatness will prevent them from moving unnecessarily when transporting the load, and it will ensure that they have the proper verticality when lifting the goods to place the pallet in the higher levels of the rack.
- Close attention to the control joints of the floor is required in order to avoid premature damage due to the intensive circulation of forklifts. There are several joints in concrete floors, the most common being control joints and construction joints. The latter are placed when there are two floors poured at different times.
2. Clear height:
- The nature of the goods, the cost-plan of renting storage space, and the quantities to be stored will define the height of the building. The higher the warehouse, the greater the storage capacity.
- New buildings for general-purpose logistic centers usually have minimum clear heights between 30 to 40 ft (9 and 12 meters) in the lowest part of the structure. This clear height helps companies to have more profitable distribution centers since having automatic and advanced storage systems increases their productivity.
3. Distance between columns:
- A good distribution center has the correct balance between the clear span (distance between columns) and the cost of the structure. The greater the distance between columns, the greater the cost of the structure. Therefore, the shorter the distance between columns, the lower the cost of the structure.
- This distance between columns must be wide enough to place aisles with racks on both sides and with enough space for the forklift to move efficiently.
4. Width of the warehouse:
- This is a very important characteristic of distribution centers since it is necessary to have adequate width to avoid wasting time during the movements of forklifts. If the width of the warehouse is greater than optimal, according to the study of estimated times for movements of goods, productivity will be lost in storage logistics.
Having an experienced designer and a general contractor is key, as they will deliver a highly efficient product that will maximize storage and not compromise your operability. Our company is a leader in the design and construction of distribution centers since we have a design team with extensive experience in this type of project.
HOW TO CHOOSE THE LOCATION FOR A DISTRIBUTION CENTER
The most important thing when determining to build a distribution center is, without a doubt, the location. This can be a decisive factor in the success or failure of the business. Before selecting the site, we recommend doing a study to determine the proximity to end customers, available utilities and infrastructure, connectivity, and local labor force.
The distribution center must have appropriate accessibility, with efficient entrances and exits and adequate connectivity to primary roads. In addition, it must be close to the city to be able to efficiently deliver to final customers and/or smaller distribution centers, known as the “last mile”, without having to waste a lot of time in traffic. This way, it will be possible to receive products from other cities and, at the same time, send them efficiently to different places.
Some of our clients have opted to design and build their distribution center with connectivity to train tracks, hoping to reduce costs by transporting their products by train instead of trucks on highways.
OUR SUCCESS STORIES IN THE CONSTRUCTION OF LOGISTIC CENTERS
At Hermosillo, we have worked alongside great clients on the design and construction of more than 100 warehouses and distribution centers all over Mexico. Each client, depending on their needs and business nature, will require specialized attributes for operations. Get to know some of the logistic centers we have built:
Chedraui: We had the opportunity to build two distribution centers for this important retail chain. These are located in Teoloyucan, State of Mexico, and in Villahermosa, Tabasco. The logistics centers were built under the fast-track, design/build scheme, and each one has a total area of 60,000 m² (645,834.63 sqft). They are “cross-docks” type, with 182 boarding docs, and have cooling and freezing chambers for the proper storage of product. At the Villahermosa distribution center, we use recycled rainwater to cool the air conditioning equipment. Thanks to these projects, we later participated in the construction of a power center with Chedraui in San José del Cabo, Baja California Sur. If you want to know more, read our blog post about this project.
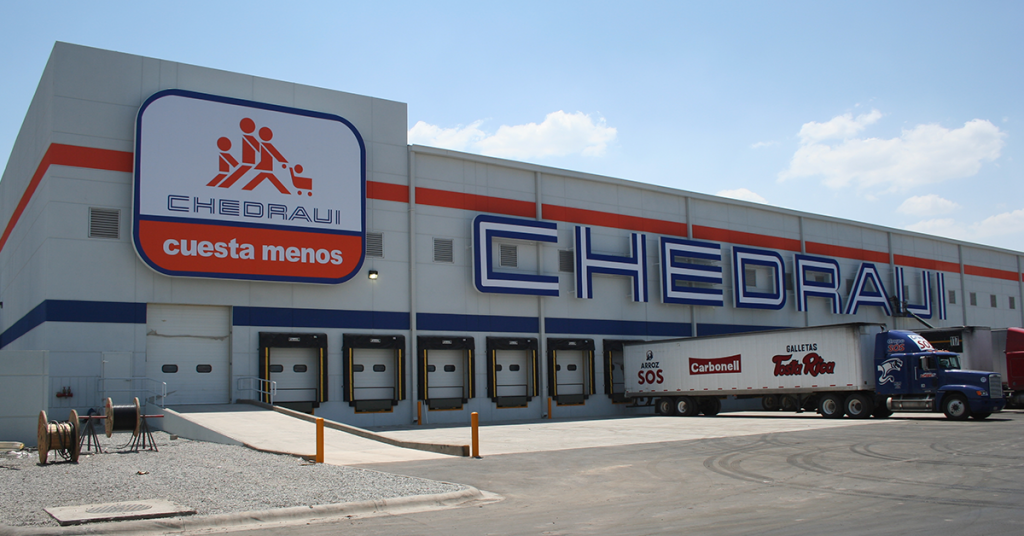
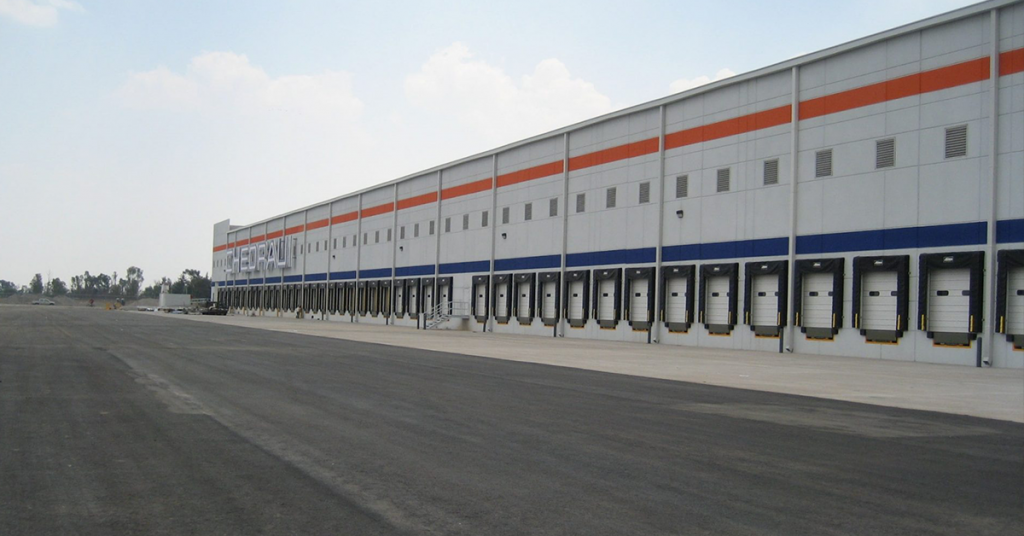
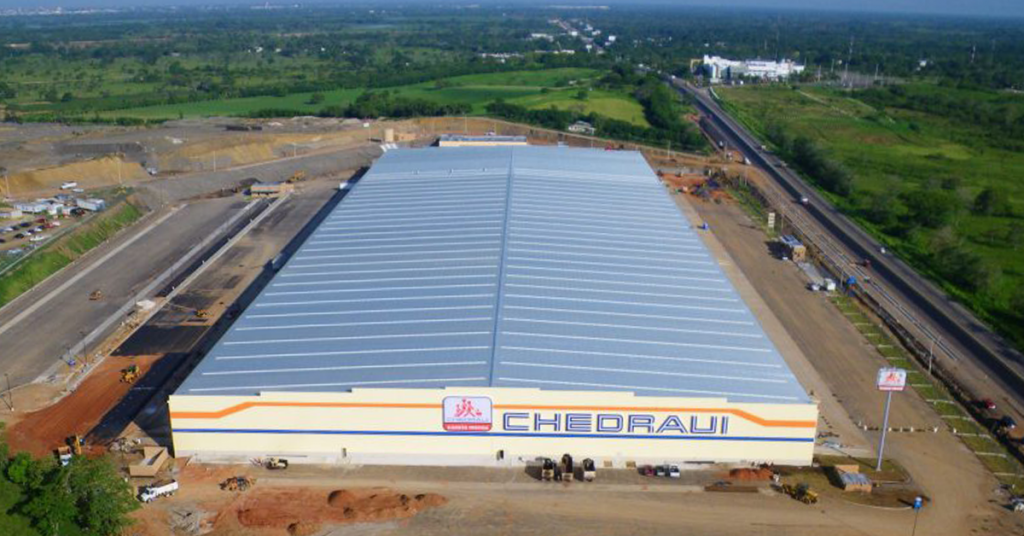
MABE: Located in Huehuetoca, Estado de México, this 70,000 m² (753,473.73 sqft) “front-dock” type distribution center was built with a connection to two different railway providers. Plus, there’s room for 69 parked train boxes and train tracks in the back.
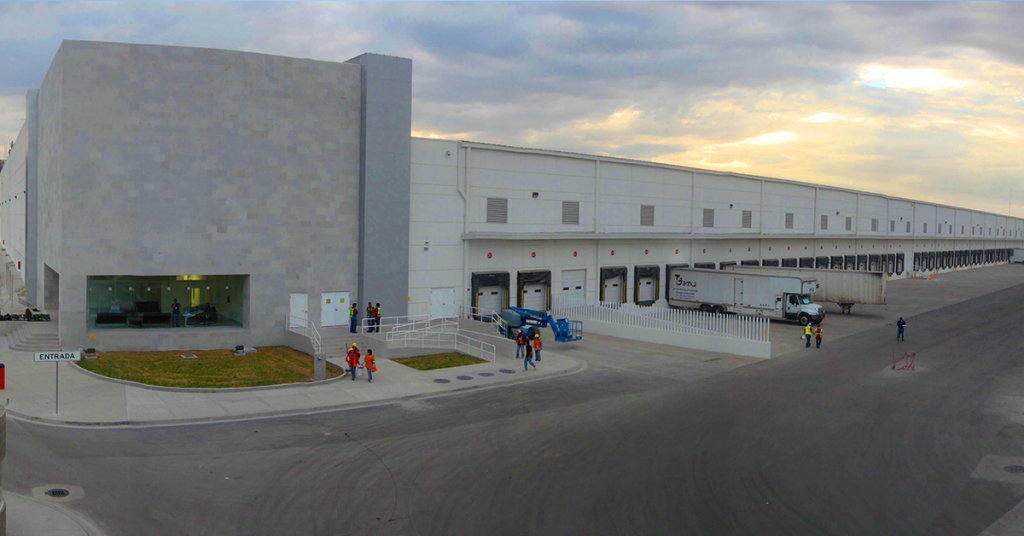
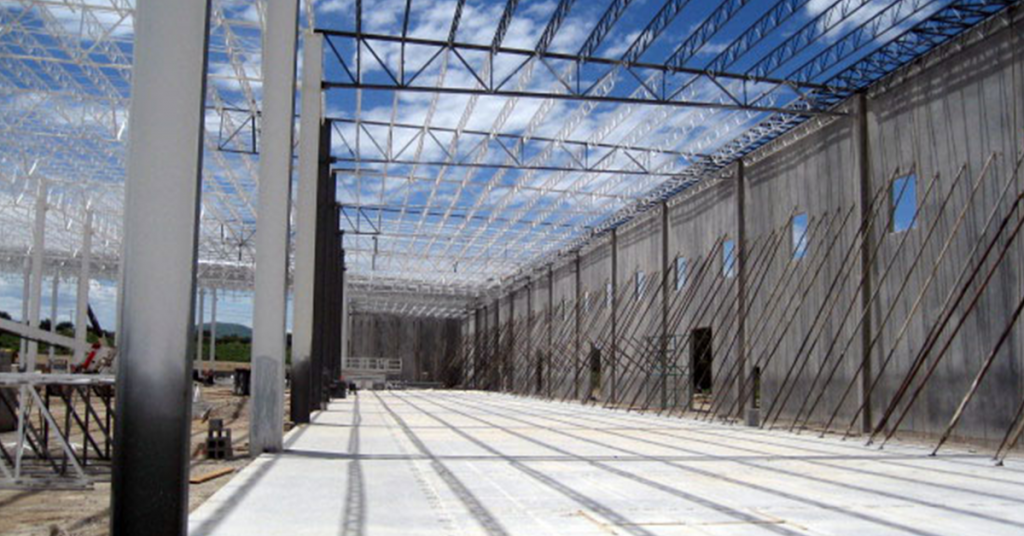
Whirlpool: This “front-dock” type project is located in Monterrey, Nuevo León. It was built with a railway spur with a length of 3.4 km, with tracks at the rear and 94 dock doors.
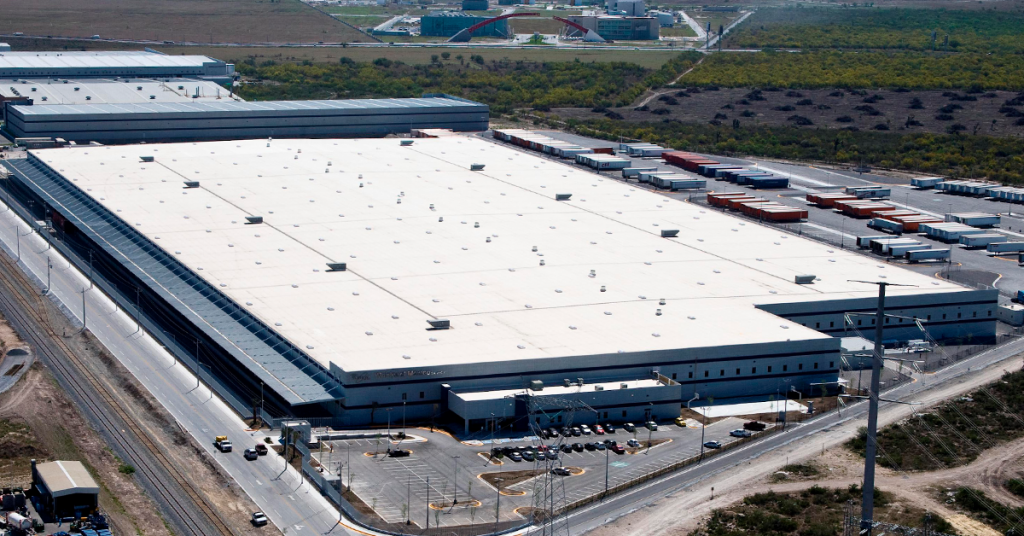
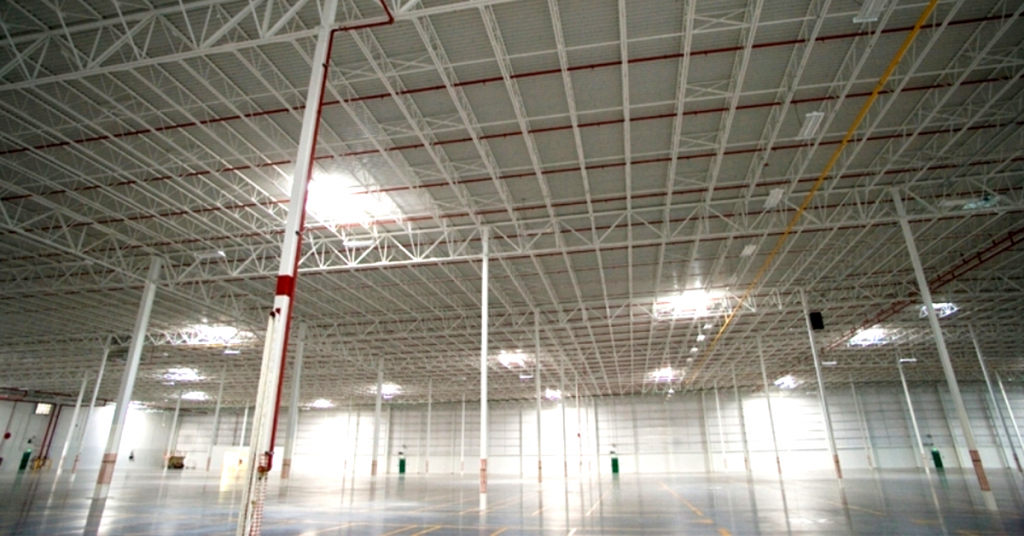
Abocol-Omagro: This was a very specialized project since the distribution center receives raw material and then mixes and stores fertilizers to later distribute to its customers. Their product arrives in a dump truck and is unloaded from below the box, falls into a pit, and is received by a conveyor. This conveyor raises it to the ceiling and from there, it drops the material into its corresponding container. This project has a total area of 14,850 m² (159,844.07 sqft).
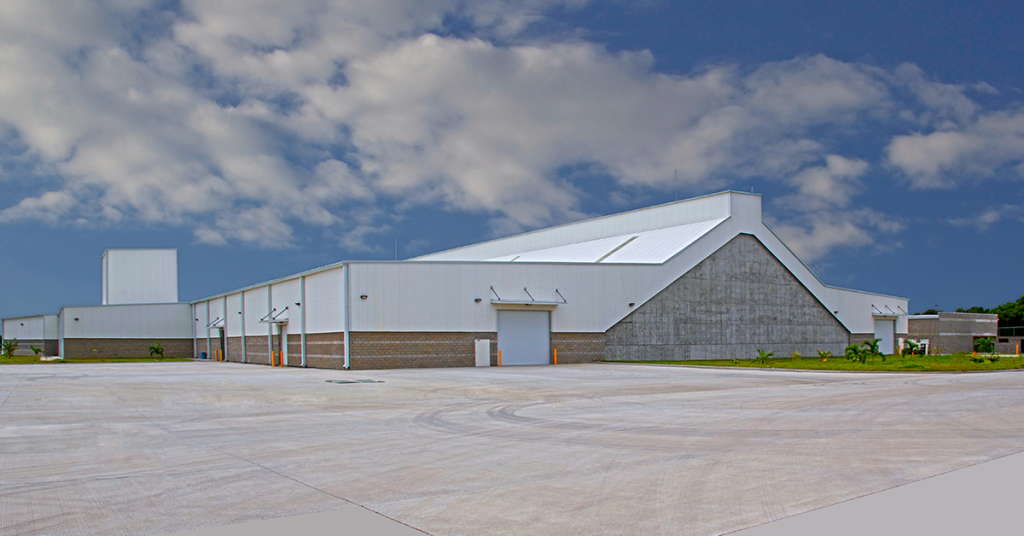
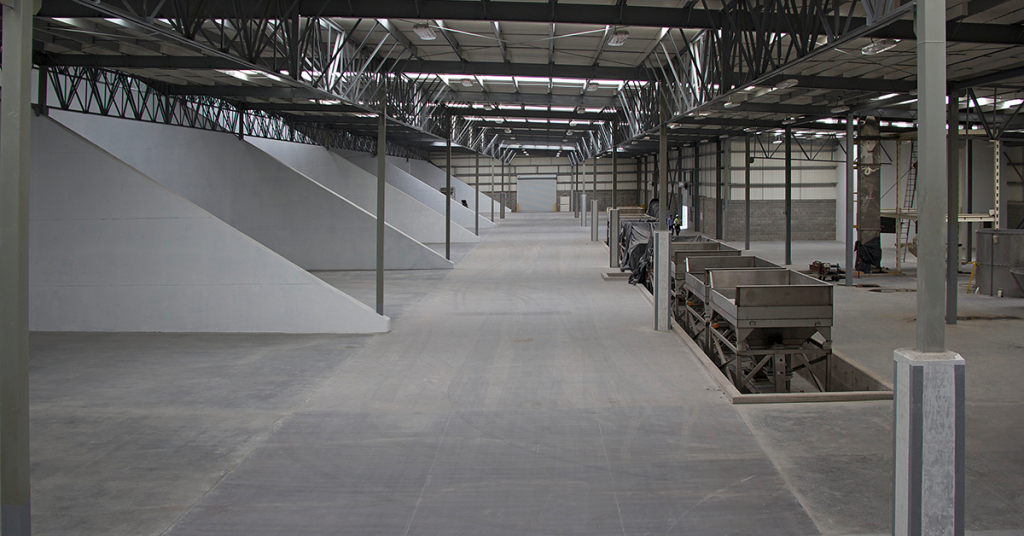
Some other of our relevant logistic and warehouse projects include:
- Walmart in Chihuahua, Chihuahua.
- The Home Depot in Atitalaquia, Hidalgo and Ciénega de Flores, Nuevo León.
- Liverpool in Monterrey, Nuevo León.
- Autozone in Jilotepec, Estado de México.
- Truper in Tijuana, Baja California.
WRAPPING UP
Every day there are more companies focused on developing their distribution chains in strategic locations in Mexico. Without a doubt, the pandemic brought challenging adjustments to everyone’s consumption behavior. This is why companies must bet on having logistics centers that are as optimized as possible, with the characteristics mentioned above. When designing and building distribution centers for our clients, at Hermosillo, we are committed to delivering a highly efficient final project that maximizes storage without compromising the operations of the companies.