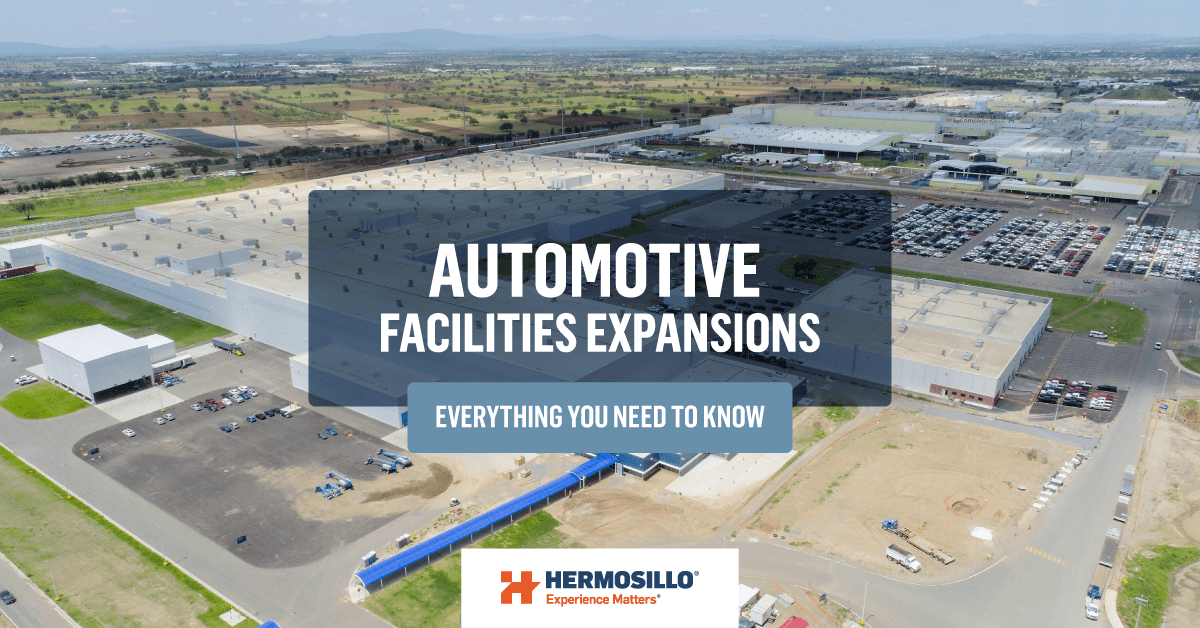
Introduction to automotive construction
The automotive industry is about precision and innovation. It’s a fast-growing and demanding business. Now more than ever, manufacturers are looking for ways to make their production plants more efficient and closer to their key markets. For instance, in 2021, Mexico produced 2,979,276 vehicles, making the country the sixth-largest global passenger vehicle manufacturer.
Furthermore, experts expect more automotive manufacturers to establish their new facilities in Mexico and/or grow the production capacity of their existing facilities, this is due to the updates made to the USMCA (United States-Mexico-Canada Agreement). It included several changes to the rules of origin for the automotive sector, such as the requirement that 75% of a vehicle’s content should be produced in North America, and that core auto parts must originate from the United States, Canada, or Mexico. As a result, these changes will provide new business opportunities for automotive manufacturers in Mexico.
So, taking into consideration the relevance of the industry, we can conclude that the functioning productivity of the facility is crucial, and there’s where we can help. We are experts in the design and construction of automotive facilities. We have built more than 90 automotive facilities since the year 2000. We are experts, and in this post, we’ll share our experience.
But first, let’s go over the types of automotive projects
The automotive manufacturing industry in Mexico is made up of seven major operations: original equipment (OEMs), aftermarket parts, electric and hybrid vehicles, remanufactured products, heavy vehicles, and other specialty motor vehicles. We will focus on OEMs, and Tier 1 and 2 suppliers.
OEMs and Tier 1 and 2 suppliers produce the components of your vehicle, such as common parts, like doors and bumpers, or more technical stuff like the exhaust systems or brake cylinders. To do so, the OEMs have different areas of production, where they manufacture some pieces, install the parts that are supplied by the Tier 1 and 2 suppliers and assemble the final vehicle.

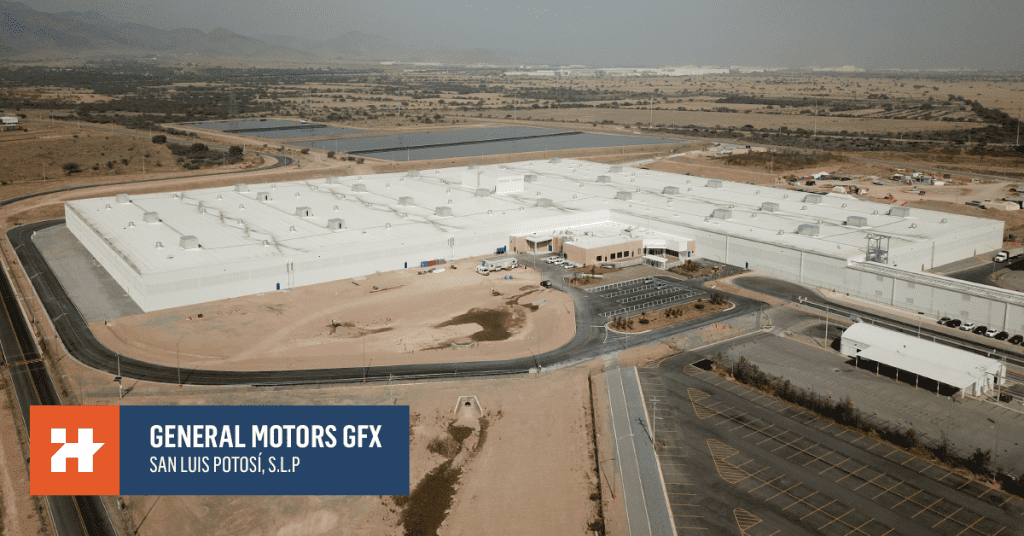
The main challenges of automotive expansion construction
The greatest challenges of expanding an automotive facility are related to its productivity. There are three which we consider being the more crucial:
- Constructing a new building expansion without stopping production of their existing plant facility. The construction process must be efficient, flexible, and focused on not interfering with ongoing production. In order to achieve this, it is necessary to thoroughly study the site and work with the production team in order to define an overall strategy that will allow the construction to be executed without compromising the production. For example, we’ve faced these situations in past projects:
- When we worked with General Motors, the conditions on the work site were very complicated. The production lines worked non-stop for 3 shifts the whole time the construction was in progress and it was needed to connect the utilities to the existing main loops located above the running production lines that had high-end robots, flammable materials, and vehicle parts in their assembly process. We also had additional challenges around the logistics and safety standards that the project required.
- Delivering the project on schedule. Automotive´s project milestones and deadlines are very critical to comply with since the production lines are scheduled to be installed and start production on a set date. Production must not be delayed and start according to plan.
- For example, when we worked with Flex-N-Gate, we achieved the goal, by completing all milestones within an ambitious 10-month design/build schedule for the complete facility.
- Projects are not defined until the end, therefore changes to the scope of work can be made. During the project’s design and construction phases, we work as a team with the end users (production team) and stakeholders of the project, having constant and flexible communication. In many cases, changes to the scope of work happen, so we should be ready to adapt quickly and propose strategies to reduce the overall impact, especially on the agreed milestones, in order for the customer to install on time their production equipment.
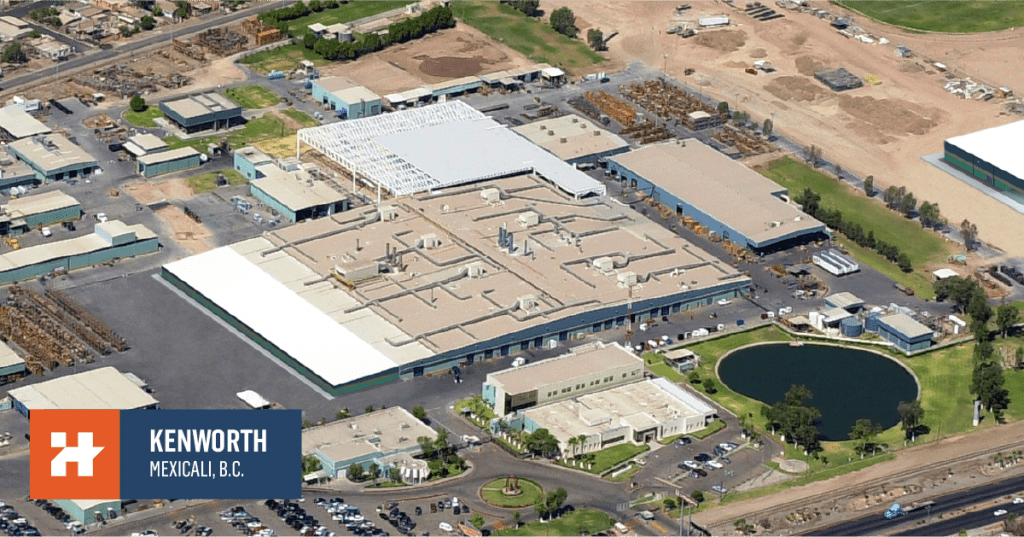
Automotive Facility Recommendations
Considering the demands that an automotive facility requires, we gathered the following recommendations that shouldn’t be absent in your project.
- Truly comprehend what your client considers “value”. When you understand it, focus your resources on delivering it throughout the project.
- The involvement of the client and end-users is of the utmost importance. In an expansion project, it’s necessary to include the plant workers, so they can give you the insights you need to protect their operation throughout the construction process.
In the following sections, we’ll specifically go through our best practices during the pre-construction and construction phases of an automotive expansion project.
About LEAN Construction Project Management
- It all starts with our Value Management workshop. Its goal is to define what’s valuable for our client and every stakeholder. Based on the results, we create a Master Plan, using the Pull Planning technique and The Last Planner System as our baselines. We review and adjust this plan monthly, or anytime in a situation that impacts the project’s course, to make the needed optimizations and to reflect its current status.
- To guarantee the correct execution, we start horizontal planning meetings, or what’s known as the Look Ahead technique. In this case, we open a 3-week specific planning schedule that allows us to accurately identify the restriction of the project and solve it accordingly.
- On the other hand, we hold Big Room sessions where every week we evaluate KPIs, progress or PPC, and the causes for no-compliance (CNCs) to tackle issues properly and on time.
- At the end of the project, we hold lessons-learned meetings with everyone involved. The purpose is to continuously improve our process and guarantee better delivery in future projects because we believe that we can always make things better.
Special requirements: concrete pits
One of the biggest challenges we faced while working with Flex-N-Gate was the construction of concrete pits to receive presses. These consisted of the edification of underground tunnels and special foundations for stamping machines.
On the other hand, when working with General Motors, we built special production pits in the stamping facility to support the stamping machines. The foundation slab was 1.20 meters thick in an area of approximately 2,500 square meters. The walls were 7 meters high and 60 centimeters thick. The pit cap slab had variable thicknesses with different metallic embeddings. Both the bases of the stamping machinery and the embedded ones were built under special requirements, and precision topography was used to meet the tolerances specified in the project. To successfully achieve this, we recommend:
- Analyze the project requirements on the workforce, materials, and equipment to comply with the assembly, falsework, casting, and stripping promptly.
- Place the prefabricated formwork, this will help improve execution times and surface quality.
- Ensure continuous concrete supply with slumps within the parameters established in the mix design approved by the designer.
- Have a second concrete pumping equipment as a backup.
Wrapping Up
With all of this in mind, we can assure you that we are the right partner for your project in Mexico, due to our international business-oriented culture, code knowledge, and local expertise that provides value to your new construction and/or expansion project. Global automotive manufacturers have trusted us to bring their vision to life in Mexico. Our expertise encompasses every single element of a highly functional automotive facility, for OEMs and their Tier 1 and 2 suppliers.