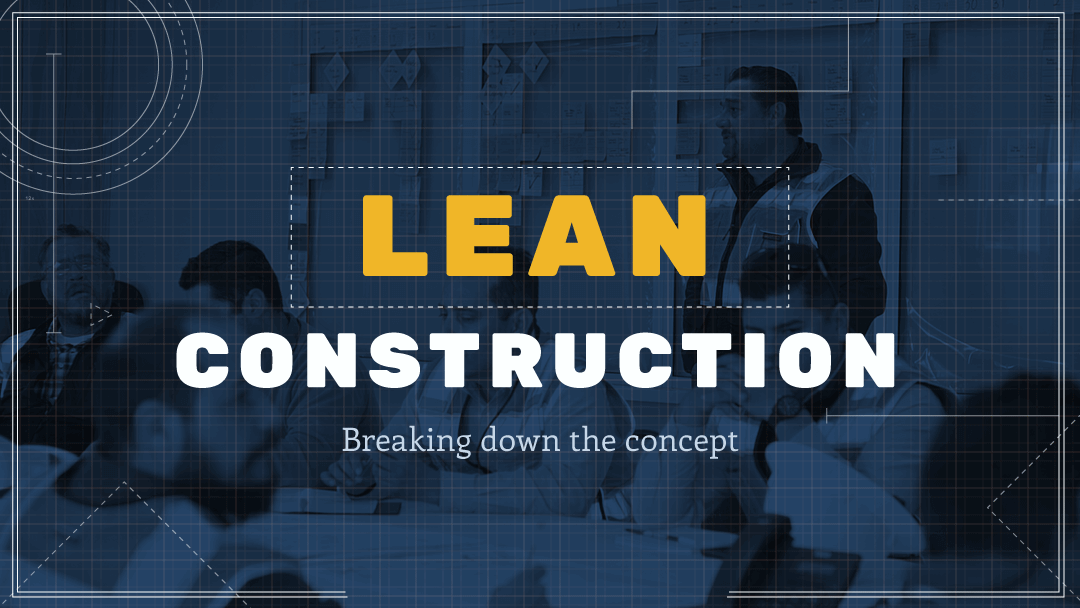
Where Does Lean Construction Come From?
To define Lean Construction, we need to discuss its origins. The first lean activities began in the manufacturing industry, specifically in the automotive sector, when F.W. Taylor and Henry Ford created the first industrial production line. This innovation established a continuous workflow that significantly reduced production time and became one of the first expressions of what we now call lean principles.
Despite being a significant step for the industry, it wasn’t until the 1950s that Toyota introduced its groundbreaking methodology, known as the Toyota Production System. In the words of its creator Taiichi Ohno, its objective was “to produce the right product at the right time in the right quantity for customer satisfaction and to produce exactly what you need and nothing more”.
Toyota set itself apart by creating a production model so efficient that its mindset has inspired a whole new way of thinking—rethinking processes, aligning with customer expectations, and rethinking their entire production system.
The said system pursued low costs, high quality, and a wide variety, allowing it to respond to customers’ desires at a swift rate. Toyota was able to introduce car personalization when the industry thought it was impossible. All of that was done by looking for better ways to do things.
Due to the success of the Toyota Production System in manufacturing, the construction industry began adopting its core principles and techniques with the same goal: to increase value and eliminate waste.
Terms like waste, value, and flow were introduced. Although lean construction may vary widely from manufacturing due to noticeable industry differences, the essence is the same. Both look for continuous optimization, collaboration, and learning, while focusing on people, creating flow, and removing things that don’t add value. More on this shortly.
What is Lean Construction?
We mentioned some interesting terms, such as people, value, waste, and continuous optimization, which are key to understanding the foundation of Lean Construction.
People are the foundation.
A Lean Construction project involves two primary audiences: the owner and the contractor. To build something, you need a team with a large set of different abilities. Therefore, you have the design team, the construction team, the purchasing area, subcontractors, and so on.
Everyone has deadlines, goals, and compromises to deliver a quality product for their client. This means that the overall result of the final product largely depends on the efficiency and coordination of all these teams. And that’s when lean practices become essential.
To coordinate and work holistically, we need to plan and respect each other’s timelines, goals, and workloads to deliver the product as promised. Lean thinking helps us focus our efforts and resources only when necessary.
For this, a wide variety of lean construction practices and tools support the planning process, creating opportunities for improvement in every phase, especially during the design and scheduling stages.
An example is when a team tries to complete a task ahead of schedule, even though the conditions aren’t ready for execution. It’s like starting gardening work when the crew is still working on tilting up the building. This has the potential to result in a waste of resources because the garden material can be damaged by the ongoing work on-site. As a result, the same task would need to be repeated, which would increase both time and cost.
This kind of inefficiency goes against core lean principles derived from lean manufacturing, where proper sequencing and coordination are essential to eliminate waste and ensure value-adding activities happen at the right time.
Waste is disrespectful.
These waste-generation activities are exactly what lean thinking expects to decrease. But you might ask: What is waste? Well, as the Lean Construction Institute states, waste is anything that doesn’t add value. “Waste is disrespectful to people; it will interfere with the environment that an individual works in and consume resources and skills.”
Value means meeting expectations.
Value, on the other hand, is anything that enhances the client’s result, meaning budget, resources, time, and overall quality of the product. In other words, it’s what the customer expects from the process.
Lean is continuous learning.
Lean thinking suggests that standardizing processes and leveling flow are the best ways to optimize a value stream. A standardized approach means more control and consistent results.
Lean Construction also suggests a mindset of continuous improvement. Experimentation is encouraged to find better ways to do things, which leads to more innovation and constant learning.
All of these dimensions must work simultaneously to achieve what lean construction is all about: removing the effort and resources that don’t create value and maximizing those that do. This creates a process with a line of experimentation to learn and adjust. It is a constant cycle.
Lean is pushing the industry to get things right from the start. (Just like we like to work)
With this in mind, Lean Construction is a methodology that respects the resources, budget, and time of the people involved in the project. It uses tools that help maximize value and reduce waste in a continuous improvement mindset.
Final thoughts
The statistics show that the construction industry still has a long way to go. Lean Construction is an approach to observing how things are done and finding a systematic path to improve them.
Here are some facts that you shouldn’t leave out:
- Focus resources and human power on activities that require it
- Limit resources and human power in activities that don’t add value
- How people work, think, and get things done will dictate whether Lean Construction practices succeed.
- Maximize value and reduce waste! Respect for all the people involved in the project, including their time, budget, and resources.
- It’s a continuous flow of finding better ways to do things, learning from them, and adapting.
- It can always be done better!
Never forget that people, value, and continuous improvement are the core of what we want to achieve.