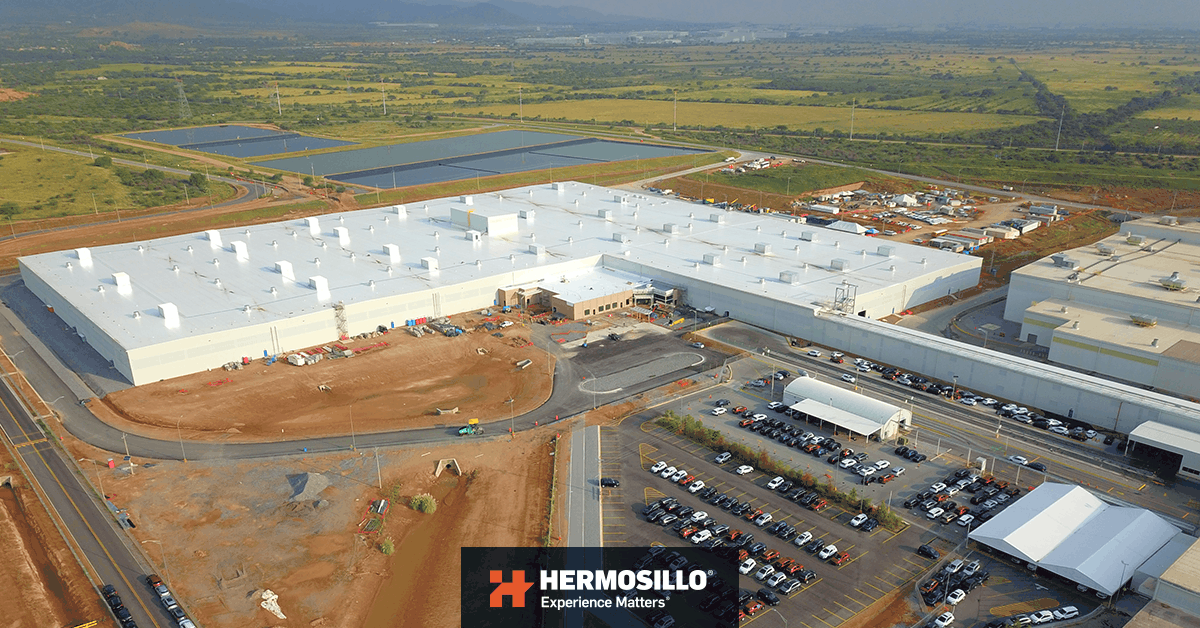
Company General Motors de México SA de CV, the Mexican branch of the American company General Motors, started operations in 1935. Currently, in Mexico, there are several GM plants with the highest productivity and quality in the world.
On January 18, 1937, directly from the assembly line, the first Chevrolet truck assembled in Mexico was born. The plant already had 222 workers and a production capacity of ten units per day.
After more than thirty years of assembly work, in 1965, GM Mexico started production of their forging, foundry, and engine manufacturing plant, located in Toluca.
Through the years, GM has relied on the quality of the workforce, the competitiveness, and the high productivity found in Mexico. For this reason, the company has continued to invest and grow its operations in its existing plants.
Project Specifications
This project, GFX Expansion – San Luis Potosí Complex, is located within the Villa de Reyes plant, San Luis Potosí, and consists of the following works:
- Body Shop Building: 54,572 m² (587,196 square feet).
- Superhighway: 1,701 m² (18,302 square feet).
- Cafeteria: 1,588 m² (17,086 square feet).
- Main Bathrooms and Truckers Office: 262 m² (2,819 square feet).
- Concrete roads and north platform: 12,058 m² (129,744 square feet).
- Paved roads, bus entrance, and parking area: 18,936.50 m2 (203,751 square feet).
Total built area: 90,819.82 m² (977,212 square feet).
Solutions and development
We developed this project along with Barton Malow, the leader in automotive construction in the United States.
The experience and far-reaching results of Hermosillo catapulted us as the ideal business partner for the execution of General Motors projects in Mexico. The role of our company throughout the project was as General Contractor.
We worked on civil-structural issues of electromechanical installations, specialized production systems, and finishes. In addition to this, Hermosillo led aspects of coordination and planning, safety, waste management, and sequencing of the different construction processes of the work. All of this is based on a culture of collaborative work and following LEAN Construction methodologies.
To meet our goal of delivering dates for each area and stage of the project in time, safety, cost, and quality, we focused on the coordination of all project participants (subcontractors and clients). For this reason, we implemented techniques such as “Last Planner”, “Pull Planning”, “Big Room”, “Look Ahead of 6 weeks”, and “Daily Huddle”.
One of the main challenges was the reinforcement of the metal roof structure in the existing Body Shop. This was necessary to have sufficient low capacity to install the new rack on the vehicle assembly line conveyor, which would be extended to the new Body Shop. The conditions in the area were very complicated, due to the fact that they had to carry out the work without suspending operation on the production lines, which worked non-stop for the 3 shifts during all the weeks.
By having the production lines running with high-end robots, flammable materials, and vehicle parts in their assembly process, a great challenge was presented due to the logistics, safety, and quality standards that the project required. All these conditions also increased the risk of generating incidents and/or accidents. However, the project reached 1,516,026 hours without incidents, generating more than 500 direct and 300 indirect jobs, approximately.
In addition to this, work was carried out in the oxidation lagoons of the wastewater in the entire complex, where high volumes of dirt roads were fixed. Finally, earthworks were done to adapt the rail tracks inside the complex and vehicle parking for the finished product.
Conclusion
The GM GFX SLP project was the second executed by Hermosillo in the San Luis Potosí complex, and the fourth for General Motors in our country. It was a great challenge. We are very proud to have participated with our partner, Barton Malow, in this important project for General Motors.